Treske Precision Machining
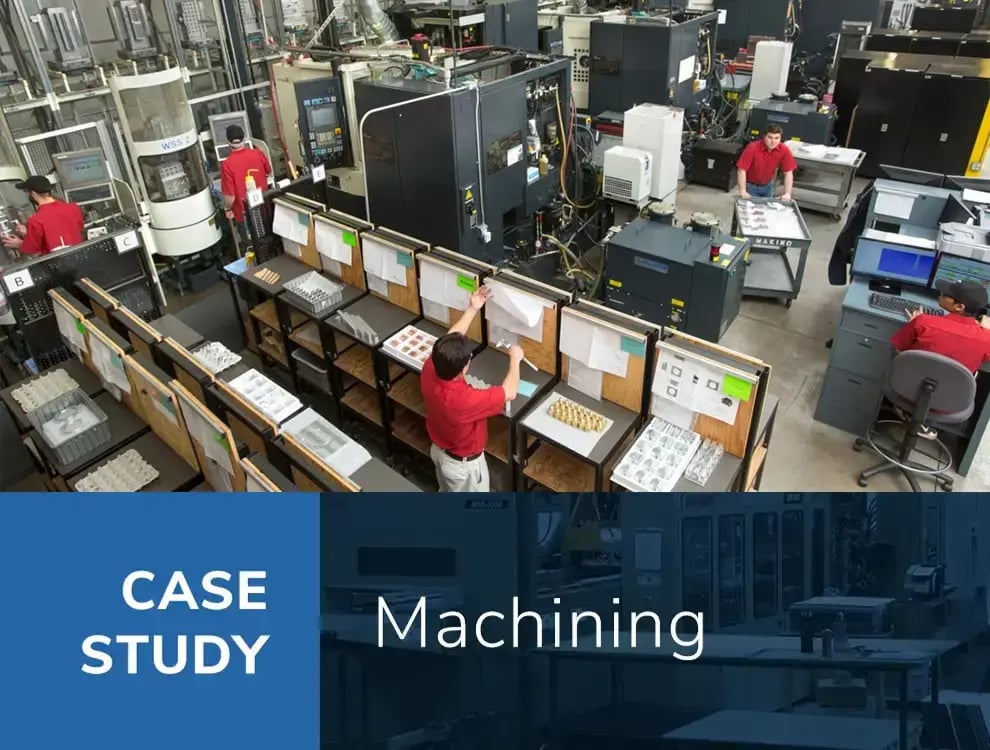
Situational Overview
Treske Precision Machining has established itself as a leader in the precision machining industry for over 40 years. The company is renowned for its superb quality and value, initially rooted in the semiconductor industry. It has since expanded its innovative systems and approaches to serve the commercial and medical sectors, as well as the aerospace and defense (A&D) industries. Treske understands the unique challenges faced by military clients and has consistently demonstrated an ability to innovate under varying conditions.
Melanie Woody is a key player at Treske Precision Machining, where she handles the expediting of parts, serves as a part packaging planner, acts as an international shipping liaison, and manages purchasing. With over 20 years of experience at Treske, Melanie contributes to multiple areas within the organization.
This case study is also available for download
Challenges
Before implementing Ready-Made Plastic Trays, Treske faced significant issues including Foreign Object Debris (FOD), loss of small parts during production, and damage to parts during transit.
These challenges necessitated the exploration of cost-effective methods to transport parts within the facility, coordinate with outside vendors, and ensure safe shipping of parts to customers while maintaining a FOD-free environment.
Actions
To address these challenges, Treske implemented Ready-Made trays with lids, designed to protect parts from environmental factors, FOD, and damage.
The decision to choose Ready-Made Plastic Trays came after thorough research on the internet. Treske required solutions that were safe, reusable, lightweight, easy to stack and store, and cost-effective for returning to customers. Committed to quality, Treske’s policies emphasize meeting customer requirements, with a strong focus on preventing FOD. The company strives to manufacture products under controlled and clean conditions.
Results
Following the integration of Ready-Made Trays, Treske observed improvements such as maintaining consistent part counts, minimized part loss, and a reduction in FOD and overall damage to parts, resulting in cost savings.
Ready-Made trays have played a crucial role in enhancing operational efficiency, facilitating safe movement of parts throughout the production floor, and ensuring secure transportation to and from outsourcing vendors. Additionally, these trays have supported Treske's Environmental Policy by aiding in recycling, reducing waste, and minimizing pollution across the company's supply chain.
Conclusion
The successful implementation of Ready-Made Plastic Trays at Treske Precision Machining has significantly enhanced the company's operational efficiency and product integrity. Treske has improved its manufacturing processes and reinforced its commitment to quality and environmental stewardship.
The use of these tailored trays has not only streamlined part handling and transportation but has also positioned Treske as a reliable partner within the aerospace and defense sectors. Ultimately, this partnership with Ready-Made has empowered Treske to maintain high standards of service and continue its legacy of innovation and excellence in precision machining.
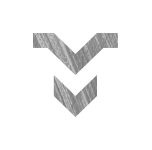
"Since using Ready-Made Plastic Trays, we have significantly improved our efficiency and reduced damage to our products. Their trays not only protect our parts but also align perfectly with our commitment to environmental responsibility."
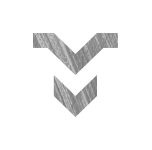
Melanie Woody
Buyer Treske Precision Machining