What Is Thermoforming?
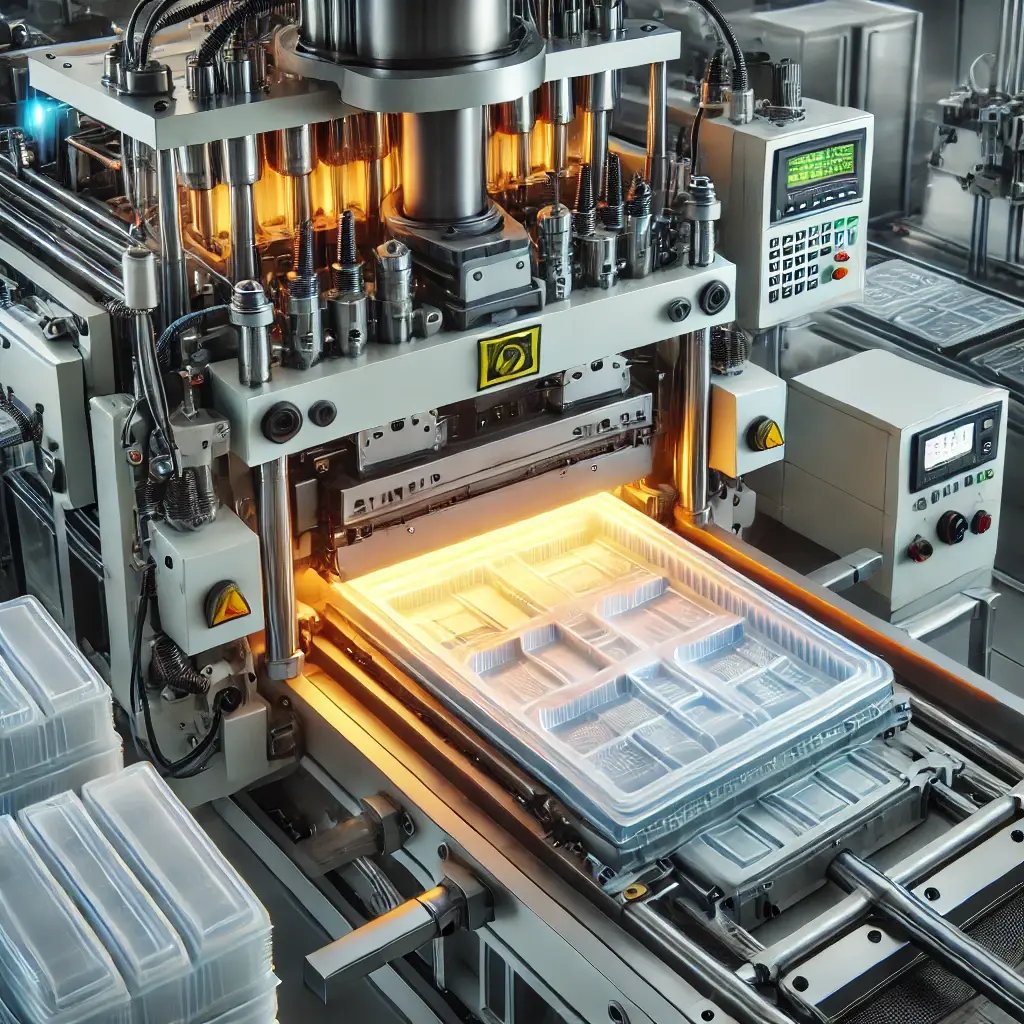
Thermoforming uses heat, pressure, or a vacuum to shape plastic materials into special forms. This manufacturing process involves heating plastic sheets and forming them over a mold. It is especially well-suited to creating lightweight packaging materials for medical devices, electronics, and household goods. Learn more about what thermoforming is and when it is used.
Types of Thermoforming
There are three main types of thermoforming: vacuum, pressure, and twin-sheet. Each uses a slightly different process to create finished products.
- Pressure forming uses vacuum suction and outside pressure to create intricate plastic shapes. It is commonly used for blister packs, medical device packaging, sports equipment, and industrial equipment.
- Twin-sheet forming produces lightweight and strong components capable of withstanding high-stress applications, such as large storage containers, air ducts, electrical enclosures, and medical device trays.
- Vacuum forming uses a vacuum to pull plastic against a mold. This is a popular choice for packaging trays, medical device blister packs, sterilization trays, and food packaging.
We can help you select the best method depending on your industry.
Common Thermoformed Materials
Common plastics used in thermoforming include high-impact polystyrene and polyethylene terephthalate (RPET). These are lightweight, durable, and cost-effective. When formed into custom shapes, they offer superior product protection, such as sterilization trays made from RPET. Because of its sustainability, we frequently use RPET at Ready-Made Plastic Trays.
Some materials have special qualities that make them well-suited to specific applications. For example, polypropylene and polyvinyl chloride offer excellent resistance to heat and chemicals. Special conductive styrene, acrylonitrile butadiene styrene, PVC, and high-density polyethylene help dissipate static buildup to protect sensitive electronics and other ESD-sensitive devices.
The Thermoforming Process
While there is some variation depending on the type of thermoforming used, each process follows similar steps. These include:
- Heating the plastic material to a temperature that allows flexibility
- Forming over a mold using vacuum, pressure, or mechanical tools
- Cooling the plastic so it retains the desired shape when hardened
- Trimming excess material and finishing the final product
Our team at Ready-Made Plastic Trays can help you find the right process and materials for your custom thermoformed trays. Contact us to get started.
Benefits of Thermoformed Plastics
Thermoforming offers many advantages for packaging materials. It creates lightweight, custom shapes that protect contents. This also reduces shipping burdens, which can help manage costs and promote sustainability. Many thermoformed plastics are food-safe, chemical- and UV-resistant, and offer electrostatic discharge protection.
Frequently Asked Questions
Many people have questions about what thermoforming is and how it works. Here are answers to some of the questions we hear most often.
What is the most common thermoforming material?
HIPS and PET are two of the most common thermoformed materials. Both can be formed in virgin or recycled versions.
Is thermoformed plastic recyclable?
Many types of thermoformed plastics are recyclable, while others are not. You should check with local facilities about requirements and to see if you will need to implement a recycling program.
Learn More About What Thermoforming Is and How It Is Used
Ready-made Plastic Trays is a leader in stock and custom thermoformed plastic trays for medical devices, automotive components, consumer electronics, household goods, and industrial applications. Contact us to explore our custom thermoforming solutions tailored to your industry needs.