Thermoforming vs. Injection Molding: Key Differences
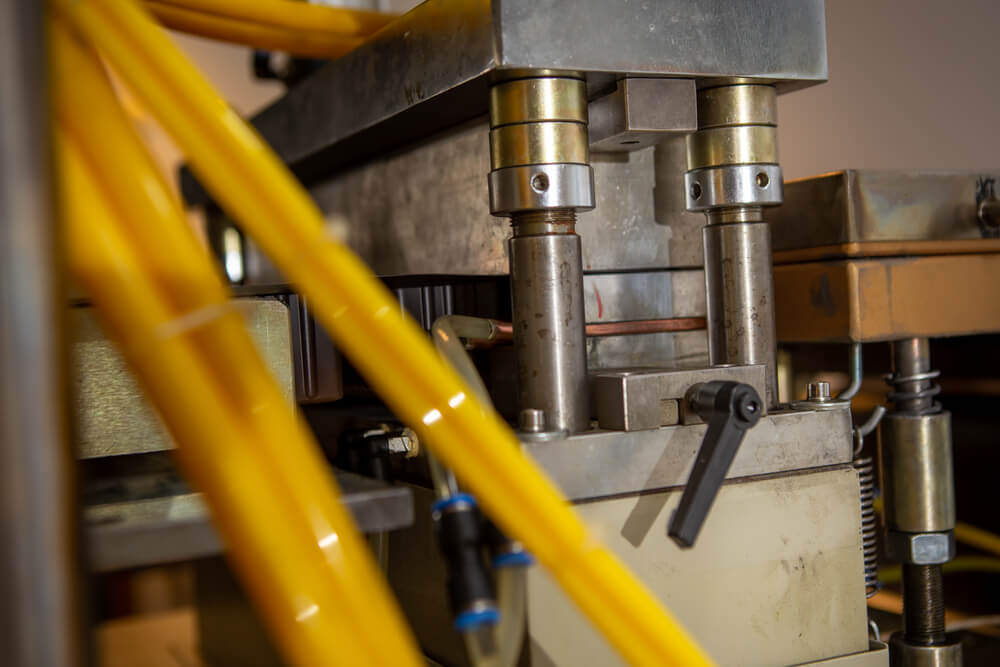
Thermoforming and injection molding are two of the most widely used plastic forming methods, shaping everything from food packaging and medical trays to automotive panels and consumer goods. But which process is best for your product? Understanding the key differences between thermoforming vs. injection molding can help you understand which is best suited for your application.
What Is Thermoforming?
Thermoforming involves heating plastic sheets and placing them on a mold. Then operators use one of several thermoforming processes to create a range of shapes. The most common are pressure and vacuum forming, which use pressure to press heated plastic sheets onto a mold. Once cooled, the plastic retains that shape permanently.
Thermoforming can create both simple and complex shapes. It is best suited for thin-walled products, such as product packaging, shipping materials, and containers. However, many manufacturers use thermoforming instead of injection molding to create other components.
Uses for Thermoforming
Thermoforming is a versatile process used for making packaging materials. However, it is also suitable for forming large sheets into plastic panels, such as those used for vehicle interiors. The most common applications for thermoforming are:
- Automotive panels
- Disposable bottles, cups, and plates
- Food packaging and trays
- Medical device packaging
- Toys
Many other household goods use thermoformed components. You can find thermoformed plastic in refrigerator trays, shower enclosures, and exercise equipment.
Thermoforming Materials
Manufacturers can use many different types of plastics for thermoforming. The right one will depend on the specific application and use environment. Some of the most popular options include:
- High-Impact Polystyrene: HIPS is one of the most popular choices for thermoformed products. It is lightweight, strong, and economical. Many of our stock shipping, medical trays, automotive, food, and beverage trays are made from HIPS, which is also available in recycled form.
- Polyethylene Terephthalate: PET is a lightweight form of polyester that is excellent for formed bottles and other general packaging. It is one of our most popular stock tray materials.
- Polyethylene Terephthalate Glycol: PETG is an environmentally conscious choice because it is highly recyclable. It is clear and flexible, making it a great choice for general-purpose formed trays and lids. A specially treated anti-static version reduces static buildup for sensitive electronics.
- Polypropylene: PP is transparent and chemical resistant. It performs well at high temperatures.
- Polyvinyl Chloride: PVC is a high-strength plastic that resists heat, grease, and impacts. Our thermoformed PVC trays are suitable for high-impact, insulated applications. It is also available in an anti-static version, which is excellent for trays and lids used for IC chips, circuit boards, and other electronics.
At Ready-Made Plastic Trays, we make stock trays from HIPS and PET. We can use various other materials to create custom plastic trays and lids for your specific needs.
Benefits of Thermoforming
One of the most significant benefits of thermoforming vs. injection molding is its cost-effectiveness, especially for smaller production runs. Its simpler setup process reduces initial tooling costs, making it ideal for projects that require flexibility, rapid prototyping, or frequent design changes.
Another key benefit is the recyclability of many thermoformed plastic materials. They tend to generate less material waste than injection molding, as excess plastic can be recycled and repurposed more efficiently. Our team at Ready-Made works to find sustainable, responsibly produced materials to support sustainability goals.
What Is Injection Molding?
Injection molding is also used to mold plastics. It is a multi-step process that has a fairly extensive setup. There are several different types of injection molding, including gas-assisted injection molding, micro-injection molding, and thin-wall injection molding.
First, designers create a mold of the desired shape. The mold is then clamped together at a specific pressure. The pressure must be able to withstand the force of the molding process.
Once it is set up, the material to be molded is heated and quickly injected into the mold cavity. The pressure of the injection process forces the plastic into every crevice within the mold. The plastic then cools and sets before it is removed.
Although injection molding requires several steps, they happen quickly. A completed part takes anywhere from a few seconds to a couple of minutes to create. This makes it a very efficient process for mass-producing precise parts.
Uses for Injection Molding
Molds allow for very intricate shapes, making injection molding a popular choice for more complex designs, such as dashboards, electronics components, and consumer goods. Some of the most common applications include:
- Automotive cup holders, outlets, door handles, and controls
- Chairs and furniture components
- Medical devices, such as plastic syringes, valves, and trays
- Plastic bottles and caps
- Utensils and kitchenware
Injection molding can produce textured surfaces, making it a great choice for mass-produced patterned items such as pet toys and ribbed bottle caps.
Injection Molding Materials
Plastics are the most commonly used injection molding material. Most thermoplastics can also be injection molded, including:
- Acrylic
- Nylon
- Polycarbonate
- Polystyrene
- Polyethylene
Some epoxies, phenolic resins, and metals including stainless steel, titanium, and copper are also suitable for injection molding.
Advantages of Injection Molding
Injection molding is a fast and efficient process that can create precise components. It is highly repeatable, so there is little to no variation from one part to the next. It can also produce finished parts that range in thickness. A major advantage of injection molding over other production methods is that it can accommodate multiple materials and colors within one piece.
Thermoforming vs. Injection Molding: Why Choose One Over the Other?
There are several considerations when comparing thermoforming vs. injection molding. The first is the complexity of your finished component design. Injection molding is typically capable of producing more intricate designs. This makes it the preferred choice for large runs of items where precision is critical, such as in creating medical equipment.
Injection molding can also produce thicker finished pieces than thermoforming. However, it has a higher upfront cost, which can be cost-prohibitive for smaller orders.
Thermoforming is very economical and is an excellent choice for simple and moderately detailed pieces. Its low upfront costs make it ideal for short runs. It has a quick setup time, which results in a short turnaround from design to delivery.
Compare Thermoforming vs. Injection Molding With Ready-Made Plastic Trays
Ready-Made Plastic Trays created stock and custom thermoformed trays for automotive, aerospace, medical, and food and beverage manufacturers. Our specialists can help you compare thermoforming vs. injection molding to determine the best solution for your needs. Contact us for a custom quote.